Folding cloth bag in the old dust bag transformation of the successful case
The new No. 1 blast furnace of the plate ironmaking plant of the Iron and Steel Group is equipped with two dust collectors and one raw material dust collector
All of them are about 2000pa, the emission exceeds 50mg/m3, the energy consumption is high and the emission is not up to standard, the group company decided to upgrade the dust collector system during the overhaul of the new 1# furnace shutdown, and the original plan was to use a conventional one
Technical transformation plan, expand the dust collector box structure, increase the number of bags to increase the original filtration area, in the iron yard, raw material dust removal system existing maintenance site to add a dust collector, the investment budget is 13.8 million
And 102.02 million, a total of 24 million yuan, while the need for supporting civil foundation building design and construction, civil construction is slow, not synchronized with the blast furnace overhaul 50-day period, supporting the design of additional equipment, manufacturing, procurement cycle is long, new primary level pipeline installation is difficult, maintenance costs increase
Maintenance costs increase, Changji equipment maintenance is not easy, in addition, production loss far exceeds the cost of technical transformation,
Bensteel steelworks organized relevant personnel to Donghua Gangte for investigation and found that Donghua Gangeh's folded cloth bags have been running for 2 years.
The dust collector's operating resistance is about 900-1100Pa, and the actual dust emission concentration is 4-8mg/nm3. After comparative analysis, the steel smelting group finally adopted the fold belt for upgrading.
The total transformation time of two iron fields and one raw material dust collector in the new No. 1 blast furnace of the iron and steel plant is 48 lines, which were put into operation on May 4, 2018.
Table 1 Comparison before and after transformation of Bensteel New No. 1 blast-furnace iron field and raw material dust collector
Pre-transformation technology
The running current of two dust collectors and one raw material dust collector is reduced by 15%-25% compared with that before the transformation. Before the dust removal transformation, the monthly electricity of each one is 1.6 million degrees, and the dust removal of raw materials is 1.3 million degrees.
Due to the improvement of the capacity of dust collector in the iron yard, the top dust pipe is incorporated into the dust collector in the iron yard, and the top fan is disabled to save electricity. A total of 510,000 yuan of electricity was saved per month and the annual benefit was 6.12 million yuan. From third party testing results
The actual dust emission concentration of 4-6mg/nm3, after the transformation of economic benefits, process benefits have been greatly improved, the transformation results are very successful.
Sum up
In this paper, the status quo of bag-type dust removal, technological innovation of pleated bag are explained, the advantages of pleated bag are analyzed, and the successful cases of pleated bag in the transformation of old dust collector are introduced. The main conclusions are as follows
(1) The filter area of the folded cloth bag is increased by 1.5-2.0 times than that of the original ordinary green two, which can greatly reduce the system resistance or pressure difference, and it is easier to clean ash, and the particle emission concentration is reduced
(2) The influence of pleated number and bag length on the flow field and resistance characteristics of pleated bag dust collector can be comprehensively considered to guide the engineering application of pleated bag with different structural parameters
(3) In the dust collector transformation, the folded cloth bag has greater economic effect and technological benefit than the traditional round cloth bag
Fold filter bag area increased 60% fold cloth bag
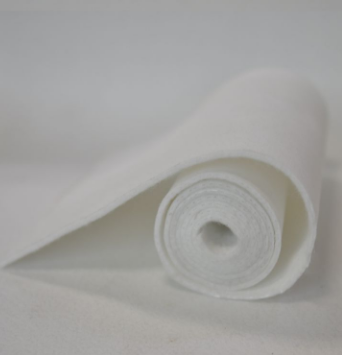